The Science Behind Porosity: A Comprehensive Guide for Welders and Fabricators
Understanding the intricate devices behind porosity in welding is essential for welders and fabricators pursuing remarkable craftsmanship. As metalworkers dive into the midsts of this phenomenon, they uncover a world regulated by various elements that affect the formation of these small spaces within welds. From the composition of the base materials to the intricacies of the welding procedure itself, a multitude of variables conspire to either aggravate or minimize the presence of porosity. In this comprehensive overview, we will certainly unwind the science behind porosity, exploring its effects on weld high quality and introduction progressed techniques for its control. Join us on this journey via the microcosm of welding blemishes, where accuracy meets understanding in the search of remarkable welds.
Recognizing Porosity in Welding
FIRST SENTENCE:
Assessment of porosity in welding reveals important understandings right into the integrity and high quality of the weld joint. Porosity, defined by the presence of dental caries or spaces within the weld metal, is a typical problem in welding procedures. These gaps, if not appropriately resolved, can jeopardize the structural stability and mechanical homes of the weld, causing potential failures in the finished item.
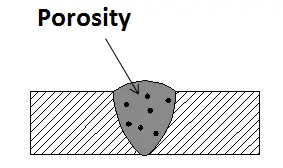
To discover and measure porosity, non-destructive testing methods such as ultrasonic screening or X-ray evaluation are frequently utilized. These techniques permit the identification of inner problems without endangering the stability of the weld. By assessing the dimension, form, and circulation of porosity within a weld, welders can make educated choices to improve their welding procedures and achieve sounder weld joints.
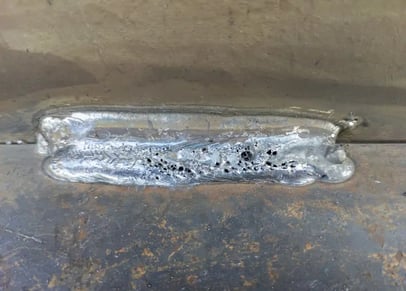
Elements Influencing Porosity Development
The occurrence of porosity in welding is influenced by a myriad of variables, varying from gas shielding performance to the ins and outs of welding parameter setups. Welding criteria, consisting of voltage, present, take a trip rate, and electrode kind, also impact porosity formation. The welding method employed, such as gas steel arc welding (GMAW) or shielded metal arc welding (SMAW), can affect porosity formation due to variations in heat circulation and gas insurance coverage - What is Porosity.
Effects of Porosity on Weld High Quality
The visibility of porosity also damages the weld's resistance to rust, as the trapped air or gases within the gaps can react with the surrounding environment, leading to deterioration over time. Additionally, porosity can prevent the weld's ability to stand up to pressure or impact, more jeopardizing the overall high quality and dependability of the bonded framework. In essential applications such as aerospace, auto, or architectural building and constructions, where security and sturdiness are paramount, the damaging impacts of porosity on weld quality can have serious effects, emphasizing the significance of reducing porosity with proper welding methods and treatments.
Strategies to Lessen Porosity
To boost the top quality of welded joints and ensure structural stability, welders and producers utilize particular strategies aimed at decreasing the formation of gaps and cavities within the material throughout the welding process. One reliable method to decrease porosity is to make sure appropriate material prep work. This includes extensive cleaning of the base steel to get rid of any kind of impurities such as oil, grease, or wetness that might add to porosity formation. In addition, making use of the appropriate welding criteria, such as the right voltage, existing, and click for info take a trip speed, is crucial in protecting against porosity. Maintaining a consistent arc size and angle during welding additionally helps in reducing the likelihood of porosity.

Furthermore, picking the ideal securing gas and preserving correct gas circulation rates are essential in lessening porosity. Utilizing the proper welding technique, such as back-stepping or utilizing a weaving movement, can also aid distribute warmth equally and decrease the chances of porosity find this development. Finally, ensuring proper ventilation in the welding atmosphere to remove any kind of prospective sources of contamination is essential for achieving porosity-free welds. By executing these techniques, welders can successfully reduce porosity and create top quality welded joints.
Advanced Solutions for Porosity Control
Carrying out innovative modern technologies and innovative methods plays an essential duty in accomplishing exceptional control over porosity in welding procedures. One sophisticated remedy is the use of innovative gas mixes. Securing gases like helium or a mixture of argon and hydrogen can aid minimize porosity by giving far better arc stability and enhanced gas protection. Furthermore, using advanced welding strategies such as pulsed MIG welding or modified ambience welding can additionally assist reduce porosity concerns.
An additional sophisticated service includes the usage of sophisticated welding devices. As an example, utilizing equipment with integrated attributes like waveform control and innovative source of power can enhance weld quality and minimize porosity risks. In addition, the application of automated welding systems with exact control over criteria can dramatically lessen porosity problems.
Moreover, integrating sophisticated monitoring and evaluation technologies such as real-time X-ray imaging or automated ultrasonic screening can browse around here aid in detecting porosity early in the welding process, permitting immediate rehabilitative activities. Overall, incorporating these sophisticated remedies can substantially enhance porosity control and improve the overall quality of welded parts.
Verdict
In verdict, understanding the science behind porosity in welding is essential for welders and makers to produce high-quality welds - What is Porosity. Advanced remedies for porosity control can better boost the welding procedure and make certain a strong and trustworthy weld.